Rotational molding offers many advantages over other plastic manufacturing processes.
Advantages of Plastic Rotational Molding
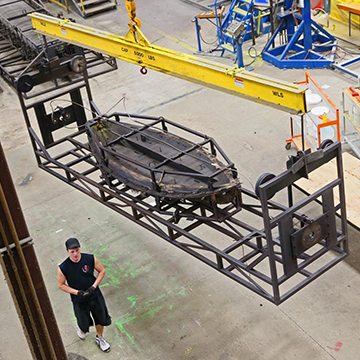
Size
Rotational molded products can be as small as a ping pong ball and as large as a 20,000 gallon tanks. Dutchland Plastics is capable of manufacturing products from 1 to 500 pounds in weight and up to 17 feet long. These parts are also more uniform and have superior strength and durability when compared to other methods like blow molding, injection molding and thermoforming.
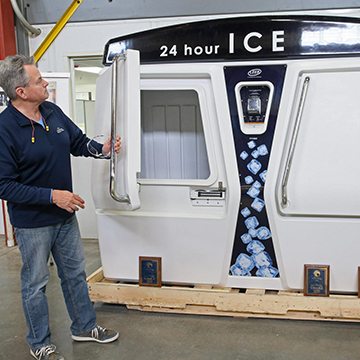
Design
Rotational molding allows much more flexibility in product design compared to blow molding. Complex shapes and moving sections are easier to manufacture and rotomolding offers a distinct advantage with uniform wall thickness.
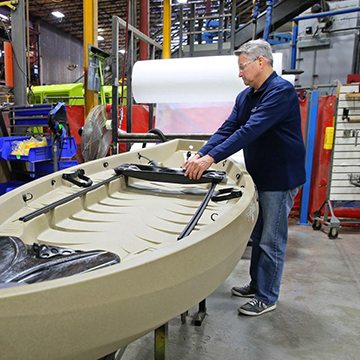
Inserts
Metal insert or threaded inserts are easily added in the rotational molding process and offer a low cost, durable and stable way to alternative assembly techniques.
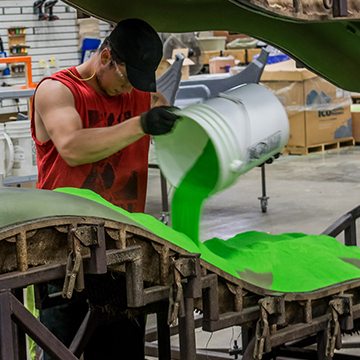
Color Sections
Dutchland offers in-house color blending to match nearly any pantone imaginable without high volume requirements. Marble, sandstone and other special colors are also available.
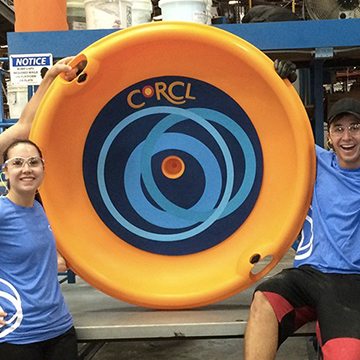
Mold In Graphics
Dutchland is highly experienced with in-mold decorating techniques that allow detailed graphics to be permanently molded into your plastic product. Items like multi colored logos, serial numbers and even bar codes are seamlessly molded into the part and are significantly better quality than traditional labels.
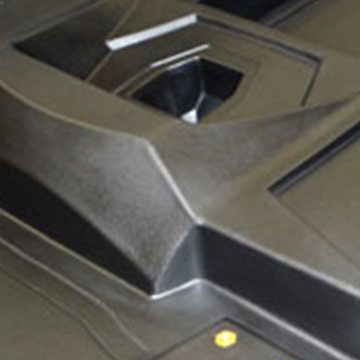
Surface Finish
From high gloss finishes to detailed textures and wood grains, rotational molding is a cast process that will duplicate any texture in the mold.
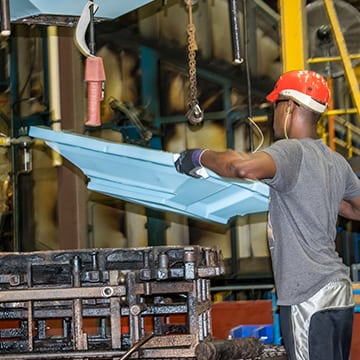
Tooling
Rotomolding is a low pressure cast process that does not require in-mold cooling or part ejection. Our molds are usually manufactured from cast aluminum making the tooling process quick and affordable. A typical lead-time for a new tooling is only 4-10 weeks depending on size and complexity and all of our molds are made locally. Aluminum Cast tooling also allows us to manufacture multiple duplicate molds to increase production capacity. In addition, tooling costs can be a lower than alternate manufacturing methods like blow molding and injection molding.
Industries We Serve
Dutchland Plastics has played a role in engineering, replicating, producing and manufacturing hundreds of products for a number of industries.
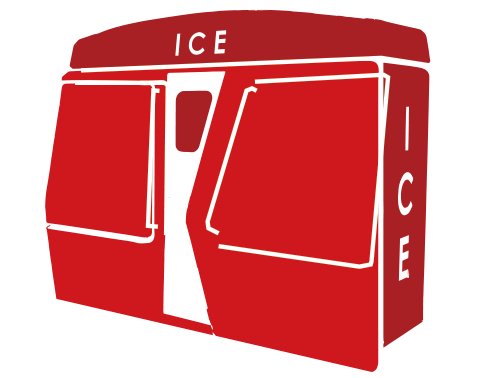
Outdoor Industry
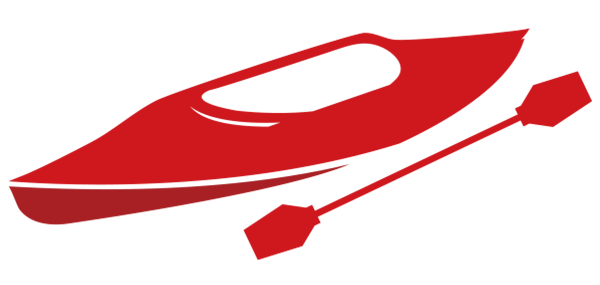
Marine Industry
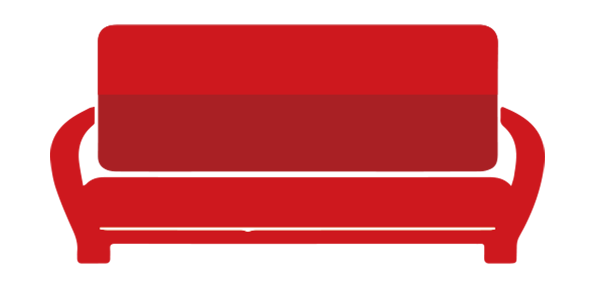